Polybutylene (Poly-B) plumbing was a popular piping material used in residential plumbing systems in Canada from the 1970s to the mid-1990s. The material was chosen because of its flexibility, ease of installation, and affordability. However, Poly-B plumbing has a notorious history of leaks and ruptures, leading to costly repairs and damage to properties. In this article, we will discuss the common issues and problems associated with Poly-B plumbing, as well as the maintenance required to prevent these issues.
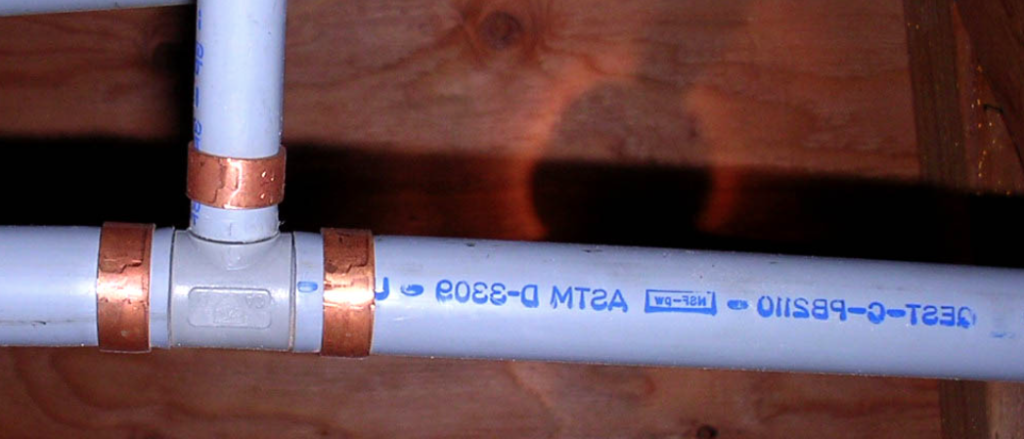
Poly-B Plumbing in Canada
Poly-B plumbing was first introduced in Canada in the late 1970s as a cheaper alternative to copper piping. The material was initially hailed as a revolutionary solution for residential plumbing systems, as it was easier to install, more flexible, and cheaper than traditional copper piping. However, it was later discovered that Poly-B plumbing had several inherent flaws that made it unsuitable for long-term use.
In the mid-1980s, reports began to emerge about leaks and ruptures in Poly-B plumbing systems, leading to extensive property damage and costly repairs. The issue was found to be caused by the material’s inherent weakness and susceptibility to degradation from chemicals, heat, and UV light. The problem became so widespread that several class-action lawsuits were filed against manufacturers and distributors of Poly-B plumbing systems.
Common Issues and Problems with Poly-B Plumbing
The most common issue with Poly-B plumbing is its tendency to leak and rupture over time. The material is prone to degradation from chemicals, heat, and UV light, which can cause it to become brittle and prone to cracking. Additionally, Poly-B plumbing systems are often installed using subpar materials, such as low-quality fittings and connectors, which can also contribute to leaks and ruptures.
Another problem with Poly-B plumbing is its susceptibility to damage from freezing temperatures. When water inside the pipes freezes, it expands, putting pressure on the pipe walls and increasing the risk of ruptures and leaks. Poly-B plumbing is also more susceptible to damage from water hammer, which occurs when water is suddenly turned off, causing a shock wave that can damage the pipes.
Maintenance of Poly-B Plumbing
To prevent issues with Poly-B plumbing, regular maintenance is essential. Homeowners should have their plumbing systems inspected by a licensed plumber every year to identify any signs of wear or damage. They should also ensure that their plumbing systems are properly insulated to prevent freezing and damage from water hammer.
In addition to regular inspections, homeowners should also replace any worn or damaged fittings or connectors as soon as possible. It is also advisable to replace any Poly-B plumbing with a more reliable and durable material, such as copper or PEX piping. While replacing an entire plumbing system can be costly, it is often a necessary investment to prevent future damage and costly repairs.
In conclusion, Poly-B plumbing is a problematic material that has caused extensive property damage and costly repairs over the years. Homeowners with Poly-B plumbing systems should be aware of the common issues and problems associated with this material and take the necessary steps to prevent them. Regular maintenance, inspections, and replacement of worn or damaged components can help extend the life of a Poly-B plumbing system, but ultimately, replacing the entire system with a more reliable material is often the best solution.